Unlike traditional desktop computers for consumers, embedded computers and edge computers are purposely built for specific software controlled applications for business operations. Especially in markets that focus on industrial automation and manufacturing, a need for an embedded computer with industrial features is in high demand. Many embedded computers play a significant role in the framework for robust compute, storage, and connectivity platforms in many Internet of Things (IoT) and edge deployments today. As the demand for faster and better computing sets the stage for greater automation, specialized computer hardware is required to ensure mission-critical reliability and real-time processing. Here are some of the most popular hardware design features to look for in embedded computers.
Requirement Checklist for Embedded Computers:
- Fanless and Silent Designs for Better Reliability
- One-Piece, Cableless, and Validated to endure Shock and Vibration
- Extended Operating Temperature Range for Harsh Environments
- Wide-Voltage Power Protection
- Modular and Expandable I/O options designed for workload consolidation

1. Fanless and Silent Designs for Better Reliability
Did you know that one of most common points of failure in a computer is caused by a faulty fan? Fans play a major role in the thermal dynamics of a computer because they dissipate heat away from critical components. For example, multi-core processors that execute sequential commands after commands have fans and heatsinks designs to cool the overall system. But once the fan stops working, components can overheat, ultimately causing the system to fail and jeopardize applications. Even though fans are a common solution to protect components from overheating, a major downfall is its long-term reliability in embedded designs. The use of fans require ventilation holes for external airflow but also opens the risks for particulate congestion from dust and debris. Overtime, these particulates naturally slip through ventilation holes and can clog internal cooling fans to a point where they fail; And once fans start to fail, critical components like the processor overheat and can be damaged. That’s why a fundamental design principle behind most embedded computers leverages a fanless and silent design. The benefit behind a fanless design for embedded computing is its proven ability to endure operations in rugged and harsh environments. By simply removing a spinning fan from the overall thermal design, this actually increases reliability and eliminates the most common point of failure that is caused by the fan.
Fanless embedded computers are completely different in design because they employ passive cooling technology and robust mechanical engineering. Passive cooling methods achieve high levels of natural air convention and thermal endurance through mechanical designs and heatsink technology. For example, embedded computer engineers leverage an aluminum-finned chassis that acts as a heatsink to transfer the heat away from critical components like the processor, all without the operation of spinning fans. In addition, copper heat pipes are also leveraged in the design to transfer a high amount of heat away from the computer system. Especially as processors and other computer components increase in performance, fanless embedded computers need to be able to support higher thermal design packages (TDP) to ensure industrial reliability in remote and mobile applications. Another benefit from a fanless design in embedded computers is its silent operation, removing the noise pollution from fans in applications that require low-acoustics.
2. One-Piece, Cableless, and Validated to endure Shock and Vibration
Most general-use computers are designed to operate in controlled environments like offices and homes. But when it comes to embedded computers, the ability to withstand many environmental challenges is also key factor in reliability. For example, many mobile IoT and remote edge deployments for in-vehicle applications leverage fanless embedded computers for the resistance to shock and vibration. Environmental factors like shock and vibration can be extremely damaging to general computers, causing failure or even harmful damage to the overall functionality. Some of the major symptoms experienced from shock and vibration are cables being unplugged, internal components displaced from sockets, and even physical damage to components itself.
Shock and vibration resistance is a key design feature that most embedded computers support through robust engineering and extensive design validation tests. High-levels of shock and vibration are so critical for embedded computers that engineers follow a strict military standard known as the “MIL-STD-810G” specification in the United States. This standard provides a fundamental guideline to ensure the environmental engineering and its testing procedures for military equipment is met. Although this standard is dedicated for military-use equipment only, embedded computer designs leverage this standard to guarantee the highest reliability and functionality for environmental challenges. For example, most embedded computers adhere to this standard by meeting shock levels up to 50G, half sine, 11ms and vibration levels up to 5 Grms, 5 - 500 Hz, 0.5 hr/axis. In order to meet shock and vibration standards here are three common design techniques used by engineers for embedded computers:
-
One-piece solid-state design: The best embedded computers are designed with the least amount of mechanical joints and pieces, usually in a single-piece design that includes the motherboard and exterior chassis. This feature is extremely beneficial to withstand environmental factors like shock and vibration because it eliminates critical points of failure from unnecessary screws and mechanical joints.
- Cableless Design: Another key distinct feature in the best designed embedded computers is the ability to offer a cableless design. The entire architecture and design fits together without any use of cables or connection to the motherboard. By removing cables from the design, this ensures all components are seated directly onto the motherboard and eliminate a common point of failure. Cableless designs are especially important in applications that experience shock and vibration.
3. Extended Operating Temperature Range for Harsh Environments
Another design principle that benefits embedded computers is the ability to operate in extended temperature ranges usually experienced in rugged and extreme environments. With the combination of fanless passive cooling and industrial-grade mechanical designs, embedded computers are the perfect solutions for its environmental resistance and long-term reliability. These type of computers are selected and deployed in the harshest applications in factory automation, in-vehicle and public transportation, outdoor kiosks, avionics, and military. Embedded engineers also follow the MIL-STD-810G standard for tailoring the equipment’s industrial design to withstand extended temperature ranges. For example, some of the best embedded computers support operating temperatures as low as 40°C and up to 70°C.
4. Wide-Voltage Power Protection
Unlike general computers that are designed for controlled environments, embedded computer designs take into account power input and voltage regulation. Integrated power protection provides an additional layer of security to safeguard electronic components from sudden voltage changes and other critical disaster situations that are often faced in mobile and rugged environments. Embedded computers need to sustain wide input voltage to cope with fluctuating power grids that spike to dangerous levels that can cause harm to the computer. For example, some of the best embedded computers support wide-voltage inputs that range from 9VDC to 50VDC. Embedded computers also include features to protect against overvoltage, overcurrent, and reverse polarity by rerouting circuits to stabilize the electronics.
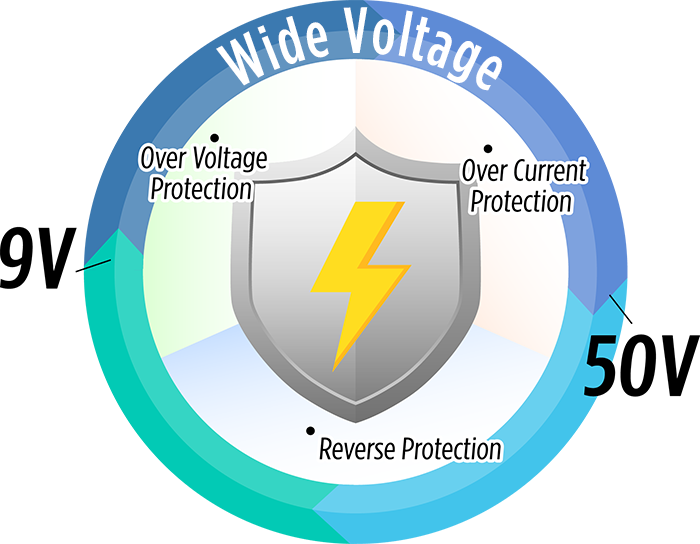
5. Modular and Expandable I/O options designed for workload consolidation
As technological advances in IoT and Edge Computing put greater demands on industries like manufacturing and automation, there continues to be a major shift of data and its value across Information Technology (IT) and Operational Technology (OT) efficiencies. This shift from the digitalization of data is shaping a competitive landscape that enables companies to condense technologies and operational workloads for scalability.
Embedded computers play a significant role for workload consolidation and convergence at the local or edge level. In other words, embedded computing systems now need to be able to manage a variety of data inputs that transmit valuable information back and forth for real-time decision making. Therefore, embedded computers need to support a variety of legacy and new input output (I/O) ports for more robust computing operations. Some of the best embedded computer designs support a multitude of legacy and modern peripheral devices with I/O port variety. In preparation for Industry 4.0, many manufacturers using traditional machinery can leverage edge computing technology to gather data analytics and insight for strategic decisions. By giving expandable options for systems integrators, rugged edge computers provide a flexible platform for integrating various sensors and actuators for the rising IoT landscape. Some of the most popular I/Os and high-speed peripherals include: USB, Serial ports, Lan/PoE, GPIO, and independent display ports. Learn more about the most popular I/O ports for embedded and industrial computing here - https://premioinc.com/blogs/blog/industrial-computer-io-ports